Speakers representing winners of the Most Innovative Knowledge Enterprise (MIKE) Awards will be speaking this week at the CII Global Knowledge Virtual Summit 2020: Knowledge in the Age of Artificial Intelligence. To be held entirely online this year from July 6 to 8, the annual summit promotes the harnessing of knowledge and intellectual capital via learning cultures, collaborative ecosystems, and leadership commitment.

YourStory is the media partner for the event and moderator of the MIKE winners’ panel. See our seven-part preview article series, which includes Knowledge Leadership, KM in the Age of AI, Gamification, Knowledge Sharing in the COVID-19 Era, and Eye on AI.
The International Judging Panel for the Global MIKE 2019 Awards consisted of Leif Edvinsson (Lund University), Constantin Bratianu (Bucharest University of Economic Studies), Bonnie Cheuk (AstraZeneca), Susanne Durst (University of Skövde), Peter Heisig (University of Applied Sciences, Potsdam), and Vincent Ribiere (IKI-SEA, Bangkok University).
Winner scores are based on eight parameters — empowerment of knowledge workers, transformative leadership, user experience, knowledge networks, innovative culture, knowledge-based offerings, knowledge creation processes, and creative spaces.
Tata Chemicals is the MIKE India and Global Winner 2019, and also won Asia’s Most Trusted Companies Award 2019. It has ranked amongst the Top 25 Innovative Companies in India; No.1 in India’s top companies for CSR, Sustainability, and Responsible Business Rankings 2019; and in the Top 10 Safe Workplaces for Women in India (by Rainmaker).
Dr Richard Lobo heads strategy, business excellence, and continuous improvement for India, the US, the UK, and Kenya operations at Tata Chemicals. A graduate of IIM Calcutta, he has been associated with the company for 11 years. He has been responsible for developing its strategies for growth in South America, Africa, Australia, and Asia (Malaysia, China, India).
Richard joins us in this exclusive interview on knowledge management processes and impacts at Tata Chemicals. He also shares tips and advice for businesses embarking on knowledge strategies.
Edited excerpts below:
YourStory [YS]: How would you describe your knowledge management (KM) journey over the years till today?
Richard Lobo [RL]: We began in the early 1950s with documentation of processes and codifying a standardised approach for operations and workplace safety. The momentum gained acceleration from then on, and by the late 1990s, we were building communities of practice (CoPs) using ISO protocols and process audits as the foundation.
By the 2000s, we adopted structured transformational programmes aimed at proactive cost focus, agile execution, collaborative innovation, and trusting relationships. Many of these programmes harnessed cross-company communities and open innovation.
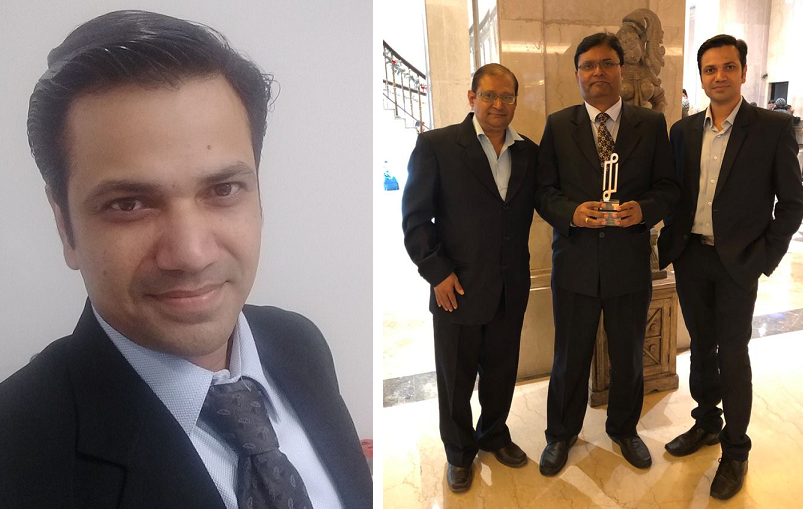
Richard Lobo and KM Team
YS: What are some impacts or metrics you can share of how KM has benefited your company?
RL: We have multiple initiatives and metrics such as percentage of ideas implemented, percentage of innovations, KM Stories, KM Day, K-Fair, InnCoTech (Innovation-Collaboration-Technology), number of best practices, and benchmark practices replicated.
Over the past many decades, we have leveraged our knowledge to grow our business. For example, the Mithapur site has expanded its capacity from a 100 TPD (tonnes per day) soda ash facility in the 1950s to 2,600 TPD today. This was possible due to knowledge of equipment design developed in-house.
A 200,000 TPA (tonnes per annum) vacuum salt production facility at Mithapur was designed and built based on past experience and knowledge of our employees. The experience of executing projects was leveraged to optimise the cost and execute it in a timely manner.
Knowledge of our employees from our North America soda ash operations was used to de-bottleneck the newly commissioned pure soda ash facility in Kenya.
YS: In which processes is knowledge is embedded in the workflow, and where is extra activity needed to manage or create knowledge?
RL: During the recent COVID-19 crisis, we used our domain knowledge of chemistry to re-align the factory to manufacture disinfectants (sodium hypochlorite) and hand sanitisers. We supplied more than 1.4 million litres and over one lakh litres of hand sanitisers for free, to various government agencies.
Tata Chemicals has leveraged nano-zinc oxide – which has anti-microbial, anti-viral and anti-fungal properties – for use in face masks in the fight against COVID-19.
Projects in R&D are categorised into Core, Adjacent, and Transformational to allow for the influx of tacit and explicit knowledge from within the company and from collaborations. This delivers science-led differentiation in our products and services.
Our safe drinking water initiative is impacting over two million households and creating employment opportunities for 1,100 village-level entrepreneurs (VLEs).
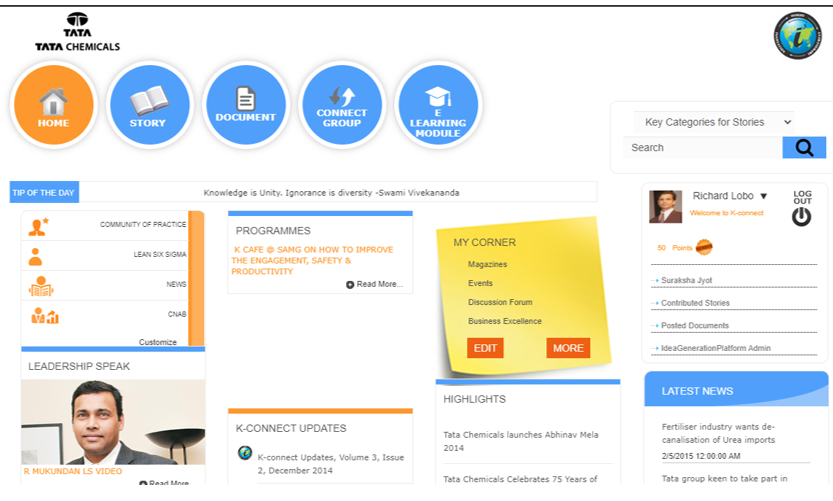
K-Connect (KM Portal)
YS: What are some communities of practice (CoPs) you have that involve knowledge inputs from external members? Are you also using crowdsourcing in this regard?
RL: We leverage CoPs extensively across our organisation. They cover safety, sustainability, maintenance, plant asset care, business excellence, Lean, Six Sigma, logistics, and supply chain. These CoPs invite industry expert views.
Senior leadership of the company serves on multiple industry bodies such as CII, as well as industry forums and R&D institutes. We also collaborate with leading institutions in India and overseas such as the CSIR labs, Yale University, IIT Bombay, Monash University, ISRO, CECRI, TERI, Strukol, and Syngene, to name a few.
Crowdsourcing is leveraged for strategically important and critical operational projects within the global Tata ecosystem, beyond the Tata Chemicals Group.
YS: It is said that KM helps incremental improvement, but 'big leap' innovation requires different teams/processes/culture. How are you structuring these two types of activities in your company?
RL: There are multiple platforms to deliver incremental and step change or big leap innovation, all delivered through cross-functional teams.
For example, structured transformation projects with defined outcomes have Lean Six Sigma and business excellence-focused programs globally. AIM (All Ideas Matter) generates 3,000 ideas per annum, delivered through Kaizen, TPM, Triz, and Theory of Constraints.
A culture of innovation leads to innovations in products and services delivered through R&D, stage-gate frameworks, and design thinking. AI and IoT also play a role here.
YS: The theme of this summit is AI and KM. What are three ways in which you are leveraging AI and analytics along with KM?
RL: We are leveraging AI and KM for transformative operational value. For example, we built a ‘digital lighthouse’ at Mithapur using industrial IoT (IIoT) and prescriptive analytics. This was used for plant operations in the boiler and carbonation towers.
We have a state-of-the-art digitally-enabled factory for nutraceuticals. We use analytics for a train-management system in our Kenya unit. Analytics for plant energy management is deployed at Tata Chemicals Europe. We also have remote sensing capability for crop health in our agri-sciences business.
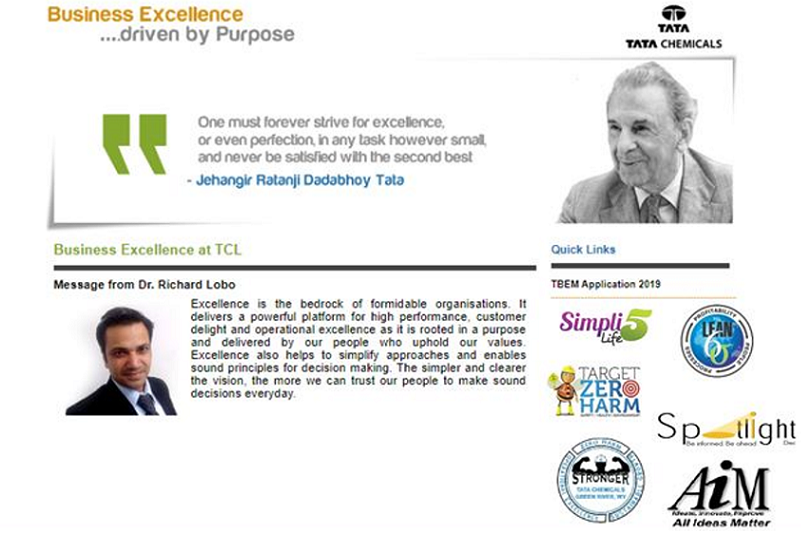
Business Excellence Portal
YS: Going ahead, how has the COVID-19 crisis impacted knowledge sharing priorities in your company? What has changed and what remains the same?
RL: Knowledge sharing has become even more crucial during the COVID-19 crisis. We began with thrice a week meetings of our Global Leadership Taskforce to share best practices across people safety and running operations amidst the pandemic.
We were able to quickly put into place SOPs with best in class practices and began monitoring three key aspects on a weekly basis: people, operations and cost.
Every Saturday, we pick one of the units of the company and share ‘Stories of Resilience’ from that unit with the Global Leadership Team. This allows an insight into how each business across the globe is shaping and re-modelling itself to deliver with excellence.
Spotlight, our competitive intelligence platform, continues to track key markets, technology, and business continuity changes across the globe.
YS: Based on your experience, what are your top three tips or words of advice on how business leaders should harness KM?
RL:
- Celebrate failure stories and broad-base the learning within the organisation. Eliminate fear of failure.
- Harness digital, AI, and KM tools to empower employees to deliver.
- Put in place metrics for safety, performance excellence, innovation and business.
(Edited by Saheli Sen Gupta)
Want to make your startup journey smooth? YS Education brings a comprehensive Funding Course, where you also get a chance to pitch your business plan to top investors. Click here to know more.
Link : https://yourstory.com/2020/07/tata-chemicals-knowledge-management-richard-lobo
Author :- Madanmohan Rao ( )
July 05, 2020 at 12:50PM
YourStory