CII’s annual knowledge summit is being held entirely online from July 6 to 8, and is titled CII Global Knowledge Virtual Summit 2020: Knowledge in the Age of Artificial Intelligence. It is also supported by the Knowledge Management Global Network (KMGN).
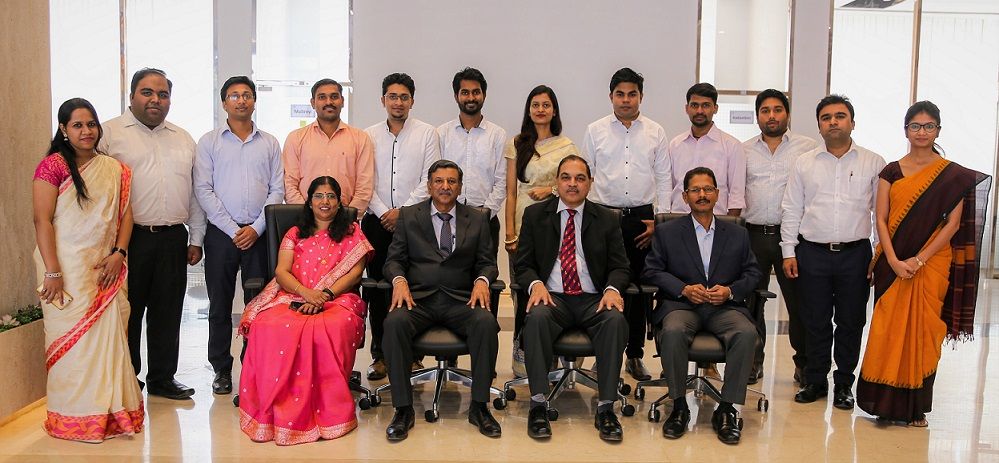
Afcons Infrastructure - Knowledge Management team
YourStory is the media partner for the event and moderator of the MIKE winners’ panel. See our seven-part preview article series, which includes Knowledge Leadership, KM in the Age of AI, Gamification, Knowledge Sharing in the COVID-19 Era, and Eye on AI.
Afcons Infrastructure is the winner of the MIKE awards at the Global, Asia, and India levels in 2019 and 2018. It earlier won the Most Admired Knowledge Enterprise (MAKE) Award in 2016 and 2017, and ASSOCHAM awards for equal opportunity enabler and talent management, Corporate Communication and PR Excellence Awards for its website, and a range of safety awards.
The Knowledge Services Group (KSG) at Afcons manages the company’s knowledge management (KM) initiative. This includes knowledge processes and culture, the Gnosis Portal, Lessons Learned Capture, Subject Matter Experts and Knowledge Ambassadors, Expert Podcasts, Project Story narratives, ‘Just-in Time’ Knowledge and Learnings, and Gamification.
Rudolf D’Souza is the Chief Knowledge Officer at Afcons Infrastructure. He also chairs the Knowledge Management Global Network, an association of KM societies from 12 nations. He was earlier the AVP (Knowledge Management) at Eureka Forbes.
Deepak Gaikwad has 25 years of experience in the construction segment, and set up the company’s quality management system. He is Joint General Manager and Head of KM and Quality, and is responsible for the knowledge culture.
C. Krishnakumari is Head of Technical Training, and has 25 years of experience in the company. She coordinated projects like the underground Metro in Delhi, jetty in Kochi, and elevated corridor in Dwarka. She now spearheads Learning and Development.
This KM team joins YourStory in a three-way conversation on Afcon’s knowledge journey, project excellence, and business impacts.
Edited excerpts below.
YourStory [YS]: How would you describe your KM journey in terms of the phases, from your early years to today?
Rudolf: Our journey can be divided into three distinct phases: start, consolidation, and embedding (processes into work). We have just entered the fourth stage, but it’s a bit early to dwell on: the benefits stage.
When it was conceptualised, Knowledge Management (KM) and Technical Training (TT) were created as new groups: KM headed by Deepak Gaikwad and TT by C Krishnakumari. Both reported into the Executive Director (Technical) Giridhar R.
Deepak: We adopted the traditional route. The GNOSIS Portal was developed on Sharepoint through the in-house IT team. We then started to populate the portal with content, domain by domain. A Knowledge Council had been formed at the head office. They used to guide us on what knowledge to capture.
Thereafter, we travelled from project to project to promote the portal and content. It was hard work at this stage. We had identified early that the ‘Learn Before, Learn During, Learn After’ model was appropriate for Afcons, being a project-based company.
We started carrying out Lessons Learned Capture and uploading them on the portal. The KM focus was on knowledge capture. The portal was for dissemination.
Krishnakumari: The idea of carving out technical training was to accelerate the capability building of our engineers. We realised that classroom training alone was not feasible. So, we opted for e-learning and were the first infrastructure company in the country to do so. It had its own challenges.
Every infrastructure company has its unique methods and philosophy. So, content had to be developed in-house by our domain experts. We now have an enviable portfolio of courses. We supplement e-learning with physical refresher courses conducted by experts at project sites.
We started Kick-off Workshops (conducted at the start of the project) and Activity Based Classrooms (conducted at the start of a key activity). It is conducted by experts organised by the TT Group. The method, sequence, resources, and so on are presented and checked by the experts. It is actually a form of ‘Just-in-time’ knowledge injection to ensure first-time right execution.
Rudolf: A couple of years back, the KM and TT Function were merged to form the Knowledge Services Group. The consolidation brought in a lot of synergies and accelerated the embedding of knowledge processes into the flow of work. Project and activity commencement is linked to activities under the ‘Learn Before’ pillar, as shown in the figure. Similarly, there are defined knowledge processes for every stage of the life cycle of the project.
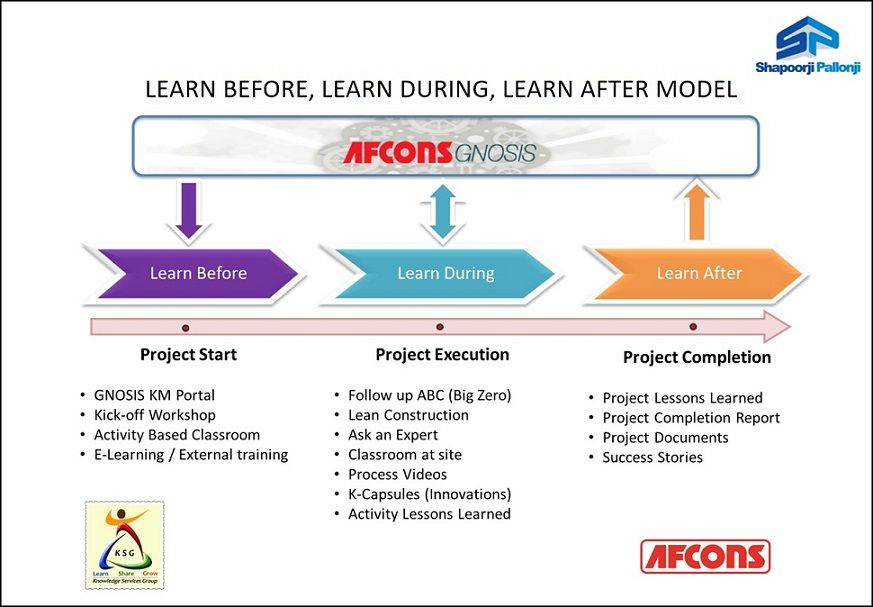
Afcons 'Learn Before, During, After' Model
YS: What are some impacts of KM on your company?
Rudolf: We do have big impact stories to share of how KM has benefited the company. The completion of India’s first twin underground metro tunnels under the Hooghly River 100 days before time is an example.
At the execution level, our focus is on transferring knowledge to engineers to execute flawlessly with improved productivity and reduced cycle times. We are also in the process of integrating Lean Construction processes into KM. Now that knowledge processes are embedded in the flow of work, the thrust this year is on visible impact in every activity.
YS: Can you give some examples of processes where knowledge is embedded in your workflows and other processes that require extra activity to manage/create knowledge?
Rudolf: As an infrastructure company, we work on large public infrastructure projects like ports, metros, expressways, bridges, and tunnels. The projects are challenging and need to be delivered in a strict time frame.
Until a few years back, the typical life cycle of a project was five years. Today, characteristically the time frame is three years, and in some cases even 24 months. This time frame includes the lean period when work is reduced because of the weather. They are monsoons (India, Africa), offshore projects, summer (India, Gulf) and winter (snowbound Himalayas).
Traditionally, a project has recourse to three resources: money, manpower and machinery. All three are in limited supply. But there is another resource – knowledge. We have some excellent processes to capture the knowledge generated and ensure it is ploughed back into the next similar activity or project.
Deepak: We use the “Learn Before, Learn During, Learn After Model”. It is linked to the commencement, execution or close-out stage of the project or major activity. For each stage, we have specific knowledge activities.
At commencement, we conduct a workshop or an activity-based classroom. The compiled Lessons Learned from a similar project are shared. Experts for that activity are brought in and over a couple of days, there is a thorough transfer of knowledge.
During execution, we run Lessons Learned capture sessions. We also have a process to study productivity and time cycles. Lean Methods of construction to improve productivity are suggested and adopted.
At the close-out stage, we again carry out Project Lessons Learned sessions, and ensure success stories and innovations are captured. For novel construction methods or challenges, we create process videos. These are high-quality 3D animations.
Rudolf: We do not leave knowledge capture and dissemination to chance. Knowledge processes are part of project execution.
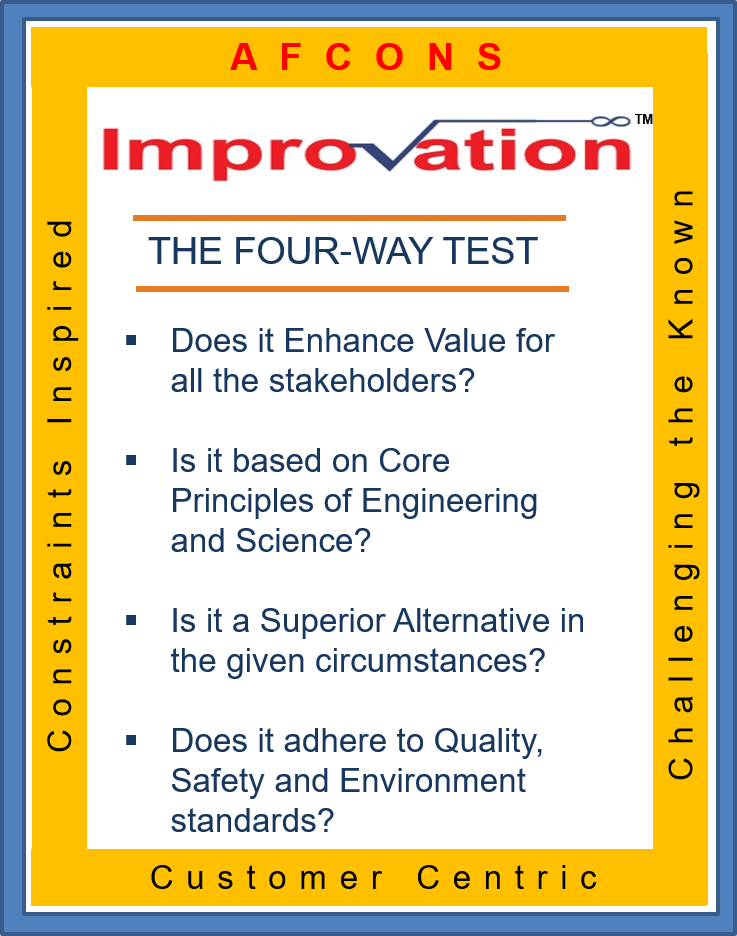
Afcons Improvation Framework
Q: What are some communities of practice (CoPs) you have that involve knowledge inputs from external members? Are you also using crowdsourcing in this regard?
Krishnakumari: A number of projects require access to the latest knowledge or getting ratifications from global sources. We have a panel of experts for each domain. They work cohesively with multiple entities around the world, such as research institutes, standards bodies, industry bodies, and suppliers. When inputs are required, they access this network.
Sometimes, joint research is undertaken, and joint papers are presented. We are also open to experimenting with new materials and providing feedback for improvement. A whole ecosystem has been assiduously cultivated over the years.
Given the nature of our business, it is prudent not to crowdsource for our core activities. Engineering and construction is a specialised field and takes years of experience to develop.
YS: It is said that KM helps incremental improvement, but 'big leap' innovation requires different team, processes, and culture. How are you structuring these two types of activities in your company?
Rudolf: Afcons has a trademarked and copyrighted innovation framework - Improvation™. It has been cultivated over the years, and is the outcome of three triggers. They are Customer Centric Innovation, Constraints-Inspired and Challenging the Known.
What we have found is that both big leap and incremental improvements are addressed through this framework. One of our big leap innovations, the ‘Retaining Wall with Reinforced Earth Wall’ has become standard industry practice. No doubt, the sheer number of incremental innovations compared to the big leap innovations will be larger, but our framework is able to cater to both.
Importantly, innovations at Afcons are developed at the point of deployment and implemented expeditiously. There is a collaborative application of knowledge, ingenuity, and sound engineering principles. When required, we leverage the expertise of the global network.
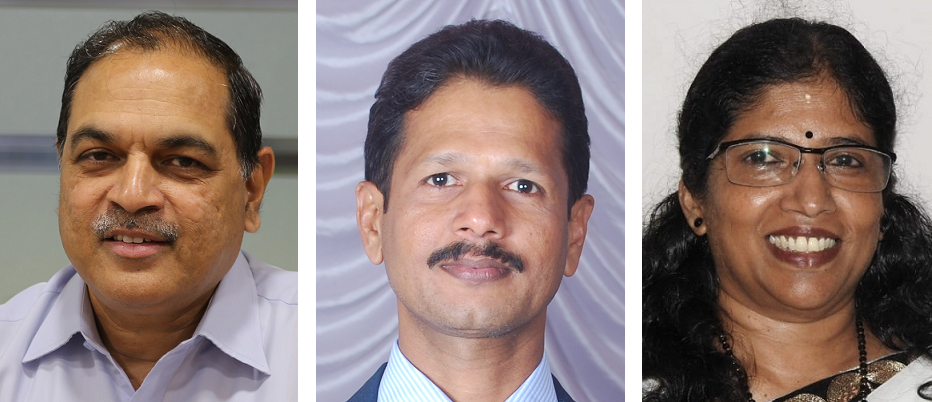
Rudolf D’Souza (L), Deepak Gaikwad, C. Krishnakumari
YS: What are some other highlights of your knowledge journey?
Deepak: This year, we have successfully created a cadre of Knowledge Ambassadors for projects. They have been given special training through a three-day bootcamp. Two days of the training was on personal effectiveness. We have invested in their long-term growth and it is paying dividends. The involvement of employees has been boosted.
Krishnakumari: We have also created a gamified environment for knowledge processes called Mission 10,000. Every knowledge activity carries points. It has been calibrated in such a way that by achieving 10,000 points in a financial year, we are assured that the project has carried out all knowledge processes as part of work.
While the points always existed, only one project had ever crossed 7,000 points in the three previous years. By creating a mission, the mindset changed and 93 percent of projects achieved this target.
(Edited by Saheli Sen Gupta)
Want to make your startup journey smooth? YS Education brings a comprehensive Funding Course, where you also get a chance to pitch your business plan to top investors. Click here to know more.
Link : https://yourstory.com/2020/07/afcons-infrastructure-knowledge-management
Author :- Madanmohan Rao ( )
July 07, 2020 at 08:37AM
YourStory